A couple of days ago I tweeted a link to a paper estimating the effect of containerisation on world trade to be far greater than the effects of trade liberalisation and GATT. It tied in with a recent post here prompted by the appearance of a shipping container in the local park. I cited there Marc Levinson’s terrific book about containerisation, [amazon_link id=”0691136408″ target=”_blank” ]The Box[/amazon_link].
It’s always a pleasure when my ramblings here get some feedback, and as it turns out Thomas Marnane, the father-in-law of a friend of mine, had a key role in the containerisation process. He’s kindly given me permission to quote his fascinating email:
“I think the container like the transistor have probably been the largest contributors to trade and communications in the world’s history.
I was fortunate to work at Matson where most of it all started. Malcolm McLean of Sea-Land actually created the first container to go with his land based trucks. Matson picked it up from there and the world followed. Matson’s historic introduction of containerization in the Pacific in 1958 launched the development of a container freight system that became a model for carriers worldwide. Matson’s S.S. Hawaiian Citizen was the world’s first all-container vessel when it was converted in 1960. Many of Matson’s innovations of that period are still in use today: cellular container ships, intermodal containers, specialized container equipment and container handling equipment.
Matson’s “A-frame” gantry crane reduced ship turnaround time in port from three weeks to 18 hours and became a prototype for the industry. …. You can see a picture of the first gantry container loading crane. It was still sitting over in Oakland when I came to Matson. It took up space and was an eyesore and the company wanted it gone. I didn’t want to simply destroy it–found no bidders in the US and no museums (Smithsonian or local) that wanted it and eventually sold it to someone in Portugal and have no idea where it is now.
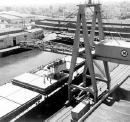
Matson’s A Frame Gantry Crane – where is it now?
I was given pretty free reign in my role as container equipment engineer and procurer at Matson and in partnership with Kiki Shahani, a very good friend and world class transpiration engineer, procured and made dozens of patentable design changes to the containers over the years. Things like changing material to stainless steel on refrigerated containers, modifications to structure and corners (lifting castings), floors, airflow, side panel shapes, paint systems, auto carriers and handling, appliances (hinges, locks, connectors for refrigeration units, etc. I say patentable because we only put patent pending on them long enough to get it to market and not have to fear that someone would steal the design, patent it and then ask for royalties. It usually took two to three years for the industry to pick up the changes through the manufacturers and incorporate them in their own equipment and by then, hopefully, we had done something better to regain a competitive edge.
The design changes were primarily to reduce damage and weight and in the case of the refrigerated containers increase temperature reliability. We were able through the growing capability of the computer to do finite element analysis and testing and determine where we needed more or less strength. The result over several years was that we achieved a reduction of about 20% in container weight and 50% in maintenance and repair. For a forty foot long dry cargo container at 8375 lbs this is a savings of 1675lbs (.2x8375lbs=1675lbs). Multiply the 1675 times any number of containers you want and you can see that the increase in load you can add to the container and thus reduction in number of containers needed and the reduced weight that ships, trucks, trains, etc have to carry is significant (cost savings, fuel savings in transporting, product damage, etc). All of this was part of my recent recognition by the University of Rhode Island for my work in resource conservation.
And just think, just like when I was a kid and loved to play with blocks, when I got to be a big boy I got to play with containers which are just really big blocks. What more could a guy want.
As you can see I still have a love affair with containers and cranes (they let me design and build cranes also with help from one great electrical engineer, Al Siver, one great mechanical engineer, Ed Stephens and a world class crane designer from Liftech, Michael Jordan–I got to travel the world with those guys and still talk with them frequently).”
And in a follow up email, having looked at the summary of the Levinson book, he added:
“I note Harry Bridges on the summary in Amazon. He is something of a legend in San Francisco (the area around the Ferry Building is called Harry Bridges Plaza) and it is still not fun to negotiate with the Longshore Union even though their numbers, as a result of containers and the handling thereof, are down by 80-90%.
Matson also had the first semi-automated system for container handling at Terminal Island, CA. It was finally abandoned because it was technically difficult to maintain and the equipment got out of date and was a big expense to replace (the business is highly capital intensive now vice labor). Some European terminals are automated (as I recall Rotterdam, Hamburg, Amsterdam and one UK Port that I cannot remember, perhaps Southampton–it has been awhile since I visited–were the leaders) and Rotterdam was the best. I got to visit them all and have exchange visits, even got the Hamburg guys to get in my hot tub!!. In the US American President Lines paved the way for intermodal (sea, truck, rail) shipping across the U.S and got us to “double stack” trains by working out routes that had overpasses, tunnels etc. in place or modified to handle the heights. I got to play with trains too when we went to moving our cargo from Seattle to Portland by train instead of having a ship come into Portland every week (the Willamette River is long and slow). We moved the cargo down from Seattle to Portland by a weekly double stack train which had to have cars modified to fit the route (some places “humping” of cars through their connections was a problem, etc.).
…. Don’t hold me too tight to the reduced container weights because it has been a while but it was at a minimum a 15% reduction and we worked on it ever year for every type of container and chassis when we placed our new container orders. Refrigerated containers got heavier with the stainless steel but the damage was reduced by more than half and the combination of less damage and subsequent less product loss was substantial. Prototype testing in Korea with Hyundai was also a lot of fun–we tried to break new designs of containers with some interesting test gear. That and leading in automating our refrigeration equipment really kept us in the game We ended up buying most containers in China–they become a commodity … as their price came down, and some of the weight reduction was the result of good thought by Chinese container engineers. Surprisingly every person in charge of container engineering in the companies we purchased from were women and they could work the drawings from behind their eyeballs vice on paper because they know their business so well.”
The close-up account is fascinating. It has also led me to reflect on what economists mean when we say – as we do all the time these days – that ‘institutions matter’ for growth. Probably most of us have institutions like trade rules and agreements in mind, but it may well be that the setting of standards and engineering principles – as in containerisation – matter much more.